Polyurethane vs. Silicone Rubber: Which is Superior?
In the realm of manufacturing and crafting, the debate between polyurethane and silicone rubber is ever-present. Both materials have their unique properties, making them suitable for specific applications. This article will delve into the differences, advantages, and applications of both materials.
Understanding the Basics
Silicone Rubber: An inorganic thermosetting polymer, silicone rubber is built on a silicon-oxygen backbone. It’s known for its excellent thermal, UV, and ozone resistance. However, it has poor tensile strength, cut and tear resistance, and abrasion resistance.
Polyurethane Rubber: An organic thermosetting polymer, polyurethane is made of a polyol and an isocyanate. It boasts excellent tensile strength, toughness, and abrasion resistance. However, its heat resistance is limited, breaking down chemically at temperatures above 80°C.
Key Differences
Chemical Structure: Silicone has a silicon-oxygen backbone, while polyurethane is made of a polyol and an isocyanate.
Heat Resistance: Silicone stands out for its excellent heat resistance, while polyurethane can only be used up to 80°C.
Durability: Polyurethane is known for its toughness and wear resistance, making it suitable for applications that require durability.
Processing: Silicone is typically processed via open mold casting, compression molding, or injection molding. Polyurethane, on the other hand, can be processed using open mold casting, rotational casting, or reaction injection molding.
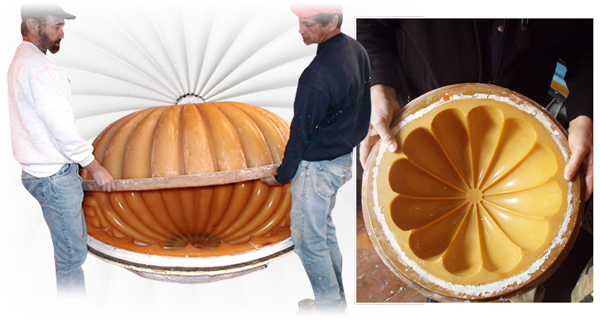
Applications VS
Silicone Rubber:
High-temperature cookware like utensils and bowls.
Molds, especially for casting polyurethane.
Industrial sealing and bonding.
Medical applications like catheters, hoses, and implants.
Seals and gaskets.
Polyurethane Rubber:
Wheels for forklifts, skateboards, and shoes.
Impact arrestors on railways and elevators.
Industrial applications like pipe linings, pump impellers, seals, molds, and conveyor belts.
Electrical potting or encapsulation.
Physical Properties Comparison
When comparing silicone and polyurethane at similar Shore hardnesses:
Hardness (Shore A): Silicone (58 A) vs. Polyurethane (70 A)
Abrasion Resistance (DIN mm3): Silicone (Not specified) vs. Polyurethane (70)
Elongation (%): Silicone (200) vs. Polyurethane (675)
Chemical Resistance: Silicone is resistant to high-temperature water, salt water, brake fluid, and chlorinated hydrocarbons. Polyurethane is resistant to fuel, oil, solvents, and weak bases/acids.
Melting Point (°C): Silicone (250°C) vs. Polyurethane (80°C)
Heat Resistance: Silicone (Excellent) vs. Polyurethane (Poor)
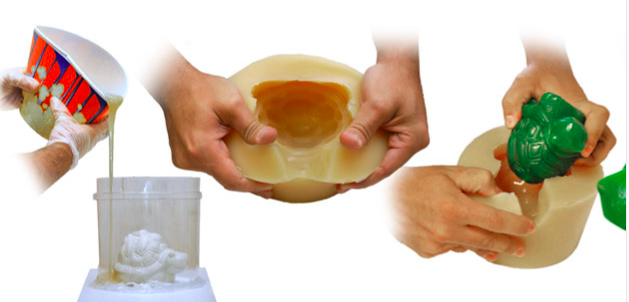
Recyclability and Sustainability
Both silicone and polyurethane are thermosetting polymers. While recycling is theoretically possible, it’s challenging due to their nature. They break down into harmful chemicals if heated past their maximum operating temperatures and don’t resolidify like thermoplastics. Currently, most recycling facilities lack the capability to recycle these materials economically. Both materials are not considered sustainable as they aren’t derived from renewable resources.
Cost Implications
Both silicone and polyurethane are advanced engineering materials and can be costly. The price depends on the grade and specific formulation used. For instance, RTV-1 silicone is relatively inexpensive, while RTV-2 silicone tends to be pricier. Similarly, cold-cast polyurethane materials are generally more expensive than hot-cast ones.
Conclusion
Both polyurethane and silicone rubber have their strengths and weaknesses. The choice between the two largely depends on the specific application and requirements. While silicone excels in heat resistance and is suitable for high-temperature applications, polyurethane stands out in terms of toughness and wear resistance. Understanding the properties and applications of both materials can guide manufacturers and crafters in making an informed decision.