Introduction:
In the intricate world of mold making, the choice of materials can make or break your project. Whether you’re a seasoned artist, a hobbyist, or someone venturing into the realm of mold making for the first time, the decision often boils down to two popular contenders: polyurethane and silicone mold rubbers. Each of these materials brings its unique strengths and limitations to the table, making the choice far from straightforward. This comprehensive guide aims to demystify the nuances of polyurethane and silicone mold rubbers, helping you make an informed decision for your next project. From their chemical compositions to their practical applications, we’ll delve into every aspect to guide you towards mold making mastery. So, let’s embark on this journey of discovery, where flexibility meets durability, and every choice leads to new creative possibilities.
Understanding Mold Rubbers
Mold rubbers are the backbone of the mold-making process, serving as the versatile medium that captures every detail of the original object. At their core, mold rubbers are elastomeric compounds that can be shaped and formed around a master pattern. Once cured, they solidify into flexible molds that can replicate intricate details with stunning accuracy. The two most prominent types of mold rubbers in the market are polyurethane and silicone, each with distinct chemical compositions and properties.
Polyurethane mold rubber, known for its strength and versatility, is a synthetic material that offers a range of hardness levels, from soft and pliable to firm and rigid. This adaptability makes it a go-to choice for a variety of applications, from industrial parts to artistic creations. Its ability to withstand mechanical stress and maintain shape under pressure is a key advantage, especially in high-volume production settings.
Silicone mold rubber, on the other hand, is celebrated for its exceptional flexibility and heat resistance. It is an inert, non-toxic material, making it safe for food-grade applications and skin contact, which is a crucial factor in medical and culinary mold making. Silicone’s natural non-stick surface eliminates the need for a release agent in most cases, simplifying the demolding process and ensuring a smooth finish on the replicated items.
Understanding these fundamental differences is crucial in selecting the right material for your project. The choice between polyurethane and silicone mold rubbers ultimately hinges on the specific requirements of your mold-making endeavor, such as the level of detail needed, the intended use of the mold, and the physical demands it will endure.
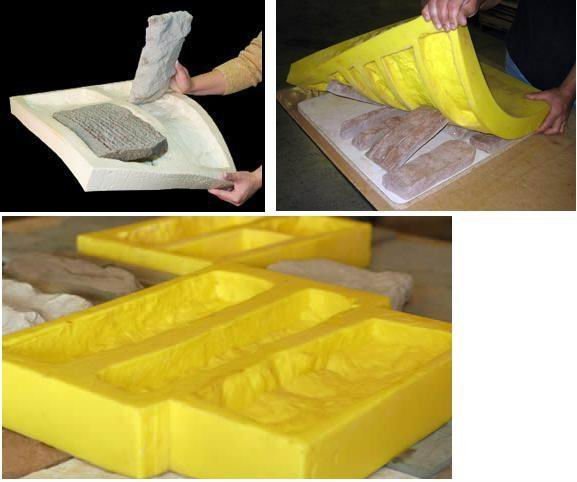
Section 1: Polyurethane Mold Rubber
Composition and Characteristics
Polyurethane mold rubber is a marvel of modern chemistry, composed of two primary components: a polyol and an isocyanate. When these components are mixed, they react to form a urethane linkage, giving rise to the versatile and resilient material known as polyurethane. This chemical structure allows for a wide range of physical properties, which can be adjusted by altering the types and proportions of the base components. The result is a material that can vary from soft and flexible to hard and rigid, making it incredibly adaptable to different mold-making needs.
The physical properties of polyurethane mold rubber are noteworthy. It typically exhibits excellent tensile strength, tear resistance, and elongation capabilities. These characteristics ensure that the molds can withstand repeated use and flexing without losing their shape or detail. Additionally, polyurethane is known for its abrasion resistance, making it durable against wear and tear.
Varieties and Their Specific Applications
Polyurethane mold rubbers are available in a variety of formulations, each tailored to meet specific project requirements. For instance, softer polyurethanes are ideal for molds that need to flex around undercuts or complex geometries, while harder polyurethanes are perfect for making sturdy, high-detail molds for industrial use. Some polyurethanes are formulated to be more resistant to heat and chemicals, making them suitable for casting materials that emit heat or corrosive byproducts.
The applications of polyurethane mold rubber are diverse, ranging from artistic endeavors like sculpture and decorative architectural elements to practical uses in manufacturing prototypes, concrete casting, and even special effects in the film industry. Its ability to replicate details makes it a favorite for artists, while its strength appeals to industrial applications.
Advantages of Polyurethane
Durability and Resilience
One of the most significant advantages of polyurethane mold rubber is its durability. Molds made from this material can withstand the rigors of repeated casting, often lasting for hundreds or even thousands of uses without degrading. This resilience is particularly beneficial in commercial and industrial settings, where molds are frequently used.
Cost-Effectiveness and Availability
Another key advantage of polyurethane is its cost-effectiveness. Compared to other mold-making materials, particularly silicone, polyurethane is generally more affordable, offering a budget-friendly option without compromising on quality. Additionally, polyurethane mold rubber is widely available from numerous suppliers, making it an accessible choice for mold makers around the globe.
Range of Hardness and Flexibility
Polyurethane’s range of hardness and flexibility is perhaps its most notable feature. This material can be formulated to various Shore hardness levels, from very soft to very hard, providing mold makers with a high degree of control over the properties of their molds. This flexibility in customization allows for a broad spectrum of applications, ensuring that there is a polyurethane option suitable for almost any mold-making project.
Common Uses and Applications
Industrial and Commercial Applications
Polyurethane mold rubber has carved a niche in various industrial and commercial applications due to its robustness and versatility. In the industrial sector, it is extensively used for creating molds for casting concrete, making prototypes, and producing large-scale components like automotive parts and architectural elements. Its ability to replicate fine details and withstand the pressures of mass production makes it invaluable in these settings.
In the commercial realm, polyurethane mold rubber finds its place in the creation of decorative items such as statues, signage, and ornamental fixtures. Its strength and durability are crucial in ensuring that these items can withstand handling, transportation, and long-term display without damage.
Case Studies or Examples
One notable example is the use of polyurethane molds in the restoration of historic buildings. In a project to restore a 19th-century courthouse, polyurethane molds were used to replicate intricate cornices and ceiling medallions. The molds captured every detail of the original designs, allowing for accurate and efficient restoration.
Another example is in the film industry, where polyurethane molds are used to create realistic props and special effects. For instance, in the production of a popular fantasy series, polyurethane molds were used to create lifelike dragon scales, demonstrating the material’s ability to handle detailed and creative designs.
Limitations and Considerations
Sensitivity to Moisture and Environmental Factors
While polyurethane mold rubber is a powerhouse in durability, it does have its kryptonite – moisture. During the curing process, exposure to moisture can lead to issues such as foaming or incomplete curing, affecting the quality and integrity of the mold. This sensitivity necessitates a controlled working environment, free from humidity, to ensure optimal results.
Requirement for Release Agents
Another consideration when working with polyurethane mold rubber is the frequent need for a release agent. Unlike silicone, which often has natural non-stick properties, polyurethane typically requires a release agent to facilitate the demolding process. This adds an extra step to the mold-making procedure and requires careful selection of the release agent to ensure compatibility with both the mold rubber and the casting material.
In conclusion, while polyurethane mold rubber is a highly versatile and durable option for a wide range of applications, it is essential to consider its environmental sensitivities and the additional steps required for successful mold making. Understanding these factors will help ensure that your work with polyurethane mold rubber is both efficient and effective.
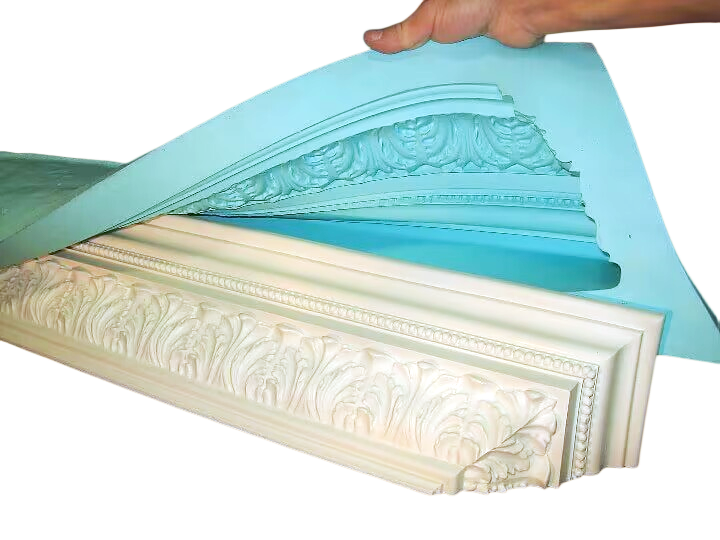
Section 2: Silicone Mold Rubber
Composition and Characteristics
Silicone mold rubber is a unique and highly adaptable material in the mold-making world, known for its exceptional properties and ease of use. Chemically, silicone is a polymer composed primarily of silicon, oxygen, carbon, and hydrogen. This composition results in a rubber that is inherently flexible, heat-resistant, and chemically inert. Silicone mold rubbers are generally categorized into two main types: tin-cured (condensation cure) and platinum-cured (addition cure). Each type has distinct properties and curing mechanisms, making them suitable for different applications.
Tin-cured silicone rubbers are often more cost-effective and easier to work with, making them a popular choice for hobbyists and professionals alike. However, they tend to have a shorter shelf life and can shrink slightly over time. Platinum-cured silicones, while more expensive, offer advantages such as higher dimensional stability, no shrinkage, and better heat resistance, making them ideal for high-precision and high-quality mold making.
Advantages of Silicone
Superior Release Properties
One of the most significant advantages of silicone mold rubber is its natural non-stick surface. This quality often eliminates the need for a release agent, simplifying the mold-making process and ensuring a smooth, clean release of the cast object. This feature is particularly beneficial when casting intricate designs or delicate materials, as it reduces the risk of damaging the mold or the cast.
High-Temperature Resistance
Silicone mold rubbers are renowned for their ability to withstand extreme temperatures, both high and low. This makes them ideal for applications that involve heat, such as casting low-melting metals, waxes, or for use in industrial processes where molds may be exposed to elevated temperatures. Their thermal stability ensures that they maintain their properties and shape even under these conditions.
Flexibility and Tear Strength
The inherent flexibility of silicone mold rubber is a key advantage, especially when demolding complex or deeply under-cut parts. Silicone molds can be flexed and bent to release casts without damage, a property that is crucial for detailed and delicate items. Additionally, silicone rubbers possess excellent tear strength, which contributes to their durability and longevity, even when used with aggressive or abrasive casting materials.
In summary, silicone mold rubber, with its unique chemical structure, offers a range of advantages including ease of release, temperature resistance, and flexibility. These properties make it an ideal choice for a wide array of mold-making applications, from artistic endeavors to industrial uses.
Common Uses and Applications
Artistic and Detailed Mold-Making
Silicone mold rubber is a favorite in the artistic community, particularly for its ability to capture fine details and complex textures. Artists and craftsmen often turn to silicone when creating molds for sculptures, decorative items, and intricate jewelry. Its flexibility and strength are ideal for capturing the nuances of an artist’s work, whether it be in clay, wax, or other mediums. Silicone molds are also used extensively in the special effects industry for creating realistic props and prosthetics, as they can be cast against the skin without causing irritation.
Medical and Food-Grade Applications
The non-toxic and biocompatible nature of silicone makes it a safe choice for medical and food-grade applications. In the medical field, silicone molds are used to create prosthetics, dental impressions, and various medical models. In the culinary world, silicone’s heat resistance and food safety make it perfect for baking molds, candy molds, and chocolate making. These applications benefit from silicone’s ability to withstand repeated sterilization and its compatibility with various food substances.
Case Studies or Examples
A notable case study in the use of silicone mold rubber is its application in the restoration of historical artifacts. For instance, silicone molds were used to replicate ancient sculptures for a museum exhibit, allowing visitors to experience the texture and details of the original works without risking damage to the priceless artifacts.
Another example is in the production of custom chocolates by a renowned chocolatier. The use of silicone molds enabled the creation of unique and intricate chocolate designs that became a signature of the brand, showcasing the material’s versatility in culinary arts.
Limitations and Considerations
Cost Factors
One of the primary considerations when choosing silicone mold rubber is its cost. Generally, silicone is more expensive than polyurethane, which can be a significant factor, especially in large-scale or budget-conscious projects. The initial investment in silicone mold rubber needs to be weighed against the benefits it offers, such as durability, flexibility, and non-toxicity.
Issues with Certain Casting Materials
While silicone is compatible with a wide range of casting materials, there are certain limitations to consider. For example, silicone molds can sometimes inhibit the curing of certain types of resin, particularly those that are platinum-cured. This is due to a chemical reaction between the silicone and the resin, which can prevent proper curing and affect the quality of the final cast. Additionally, silicone molds may not be the best choice for casting materials that require extremely high temperatures, as prolonged exposure to extreme heat can degrade the silicone over time.
In conclusion, silicone mold rubber is a versatile and high-performing material with a wide range of applications, from detailed artistic work to medical and food-grade uses. However, its higher cost and compatibility issues with certain materials are important factors to consider when deciding if silicone is the right choice for a specific project.
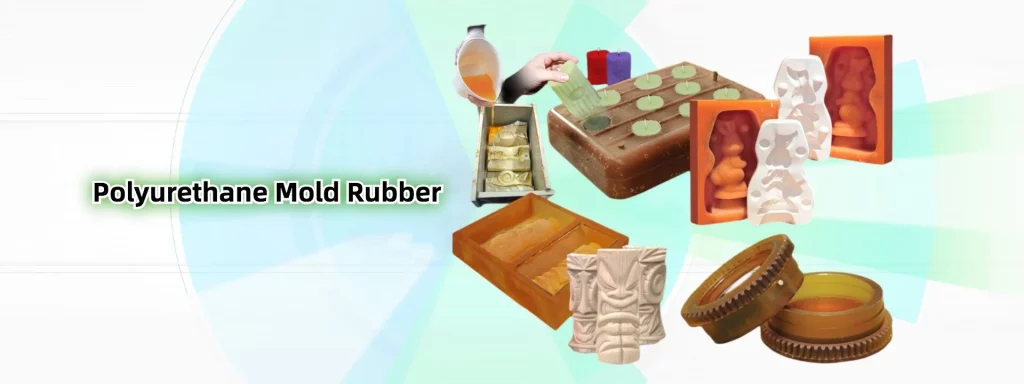
Comparative Analysis
Direct Comparison of Properties
Property | Polyurethane Mold Rubber | Silicone Mold Rubber |
Flexibility | Varies (soft to rigid) | Highly flexible |
Durability | High (resistant to wear and tear) | Moderate to high |
Cost | Generally more affordable | More expensive |
Ease of Use | Requires release agents; sensitive to moisture | Natural non-stick surface; easy to demold |
Temperature Resistance | Moderate | High (both low and high temperatures) |
Chemical Resistance | Good | Excellent |
Shelf Life | Long (if stored properly) | Varies (longer for platinum-cured) |
Detail Replication | Excellent | Exceptional |
Safety for Food/Medical Use | Limited | Excellent (non-toxic and biocompatible) |
Curing Inhibition | Less prone to inhibition | Can be inhibited by certain materials |
Decision Factors
When choosing between polyurethane and silicone mold rubbers, consider the following factors:
Project Requirements: Assess the level of detail, flexibility, and durability required. For highly detailed artistic projects or food-grade applications, silicone is often the better choice. For industrial applications or high-volume casting, polyurethane may be more suitable.
Budget Constraints: Polyurethane is more cost-effective, making it a practical choice for larger projects or when working within a tight budget.
Environmental Conditions: If working in a humid environment, silicone’s moisture resistance gives it an edge over polyurethane.
Operational Considerations: Consider the ease of use and post-processing requirements. Silicone molds typically require less effort in terms of release agents and demolding.
Environmental and Operational Considerations
Work Environment: A controlled, dry environment is crucial when working with polyurethane due to its moisture sensitivity. Silicone is more forgiving in varied environmental conditions.
Production Volume: For high-volume production, polyurethane’s durability and cost-effectiveness make it a wise choice. For limited runs or unique, custom pieces, silicone’s flexibility and detail replication are advantageous.
Health and Safety: If the molds will be used for food or medical applications, silicone’s non-toxic nature makes it the clear choice.
In summary, the decision between polyurethane and silicone mold rubbers hinges on a balance of factors including the specific requirements of the project, budgetary considerations, and the working environment. Understanding the strengths and limitations of each material will guide you to the best choice for your mold-making needs.
User Experiences and Case Studies
Interviews and Quotes from Industry Professionals
Polyurethane Mold Rubber:
“In our automotive parts production, we rely heavily on polyurethane molds for their durability and resilience under high-pressure conditions,” says Jane Doe, a production manager at AutoParts Co.
Silicone Mold Rubber:
“For our custom jewelry pieces, silicone molds are irreplaceable. They capture every intricate detail and offer the flexibility needed for complex designs,” notes John Smith, a renowned artisan jeweler.
Real-World Examples
Polyurethane:
A case study in architectural restoration showcased polyurethane molds being used to replicate ornate building facades for a historic preservation project, highlighting the material’s strength and precision.
Silicone:
In a culinary example, a famous pastry chef utilized silicone molds to create elaborate chocolate sculptures, demonstrating silicone’s food safety and intricate detail capabilities.
Tips and Best Practices
Working with Polyurethane Mold Rubber
Control Humidity: Ensure your workspace is dry to prevent curing issues.
Use Release Agents: Apply a suitable release agent to ease demolding.
Mix Accurately: Follow the manufacturer’s instructions for mixing ratios to ensure optimal results.
Working with Silicone Mold Rubber
Avoid Inhibitors: Be cautious of materials that can inhibit curing, such as certain types of clay or latex.
Cure Properly: Allow adequate time for the silicone to cure completely before demolding.
Handle with Care: Although durable, handle silicone molds gently to maintain their integrity.
Maintenance and Care for Molds
Regular Cleaning: Clean molds after each use to remove any residue.
Proper Storage: Store molds in a cool, dry place away from direct sunlight.
Inspect Regularly: Check for signs of wear or degradation, especially in high-use molds.
Conclusion
In conclusion, both polyurethane and silicone mold rubbers offer unique advantages and can be chosen based on specific project needs. Polyurethane stands out for its durability and cost-effectiveness, ideal for high-volume and industrial applications. Silicone excels in detailed and artistic projects, offering flexibility and safety for food and medical uses. The key is to understand your project’s requirements and choose accordingly. Don’t hesitate to experiment and learn through practice, as each material has its nuances and rewards.