Introduction:
In the dynamic world of product development, quick prototyping stands as a cornerstone, turning visionary ideas into tangible realities at an unprecedented pace. At the heart of this rapid materialization process are two key players: silicone and polyurethane mold rubbers. Each of these materials brings its unique set of properties to the table, influencing the efficiency, quality, and feasibility of prototype development. This comprehensive guide dives deep into the world of silicone and polyurethane, unraveling their strengths and weaknesses in the context of quick prototyping. Whether you’re an experienced product designer, a budding inventor, or a curious hobbyist, understanding the nuances of these materials is crucial in choosing the right path for your prototyping journey. So, let’s embark on this comparative exploration to uncover which mold rubber reigns supreme in the fast-paced arena of prototype development.
Understanding Quick Prototyping
Quick prototyping, also known as rapid prototyping, is a revolutionary process that allows designers and engineers to create physical models of their designs in a fraction of the time traditionally required. This method transforms digital blueprints into three-dimensional, tangible objects using various materials and techniques. The significance of quick prototyping in product development cannot be overstated. It enables innovators to test and refine their designs rapidly, identify potential issues early, and showcase realistic models of their products to stakeholders and customers. This accelerated feedback loop is invaluable in today’s fast-paced market, where speed to market can be a critical competitive advantage.
Requirements for Materials in Rapid Prototyping
Materials used in rapid prototyping need to meet several key criteria. They must be versatile enough to accurately represent the design, yet robust enough to withstand handling and testing. The ideal materials should offer a balance between strength and flexibility, allowing for both durability and intricate detailing. Additionally, they should be compatible with the chosen prototyping technology and cost-effective, especially when multiple iterations are required.
Overview of Mold Rubbers in Prototyping
Introduction to Mold Rubbers
Mold rubbers are a fundamental component in the prototyping process, especially when it comes to replicating designs that require flexibility, detail, and accuracy. These materials are used to create molds into which various casting materials can be poured or injected to form the final prototype. The two primary types of mold rubbers used in prototyping are silicone and polyurethane, each offering distinct properties that can be leveraged depending on the project’s requirements.
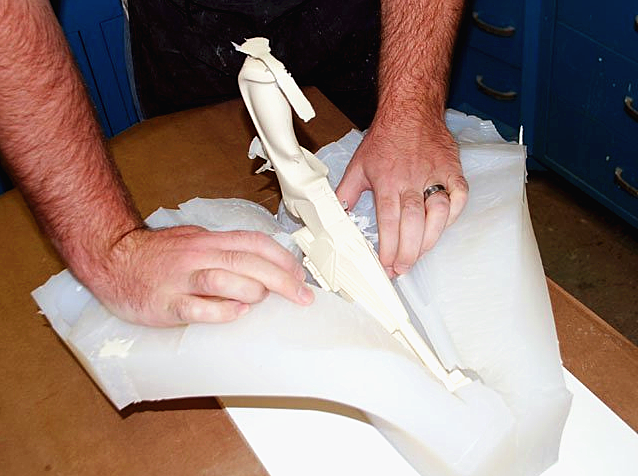
Role of Mold Rubbers in the Prototyping Process
In the prototyping process, mold rubbers serve as the bridge between a digital design and a physical model. They are used to create molds that accurately capture the intricate details of a design, allowing for the production of multiple copies of a prototype with consistent quality. Mold rubbers like silicone and polyurethane are particularly favored for their ability to reproduce fine details, their ease of use, and their adaptability to various casting materials. Whether it’s for validating a design, conducting user testing, or presenting a concept to investors, mold rubbers play a crucial role in bringing ideas to life in the physical world.
Section 1: Silicone Mold Rubber in Prototyping
Composition and Properties
Silicone mold rubber, a mainstay in the prototyping world, is distinguished by its unique chemical makeup and physical characteristics. At its core, silicone is a polymer, primarily composed of silicon combined with oxygen, carbon, and hydrogen. This composition results in a material that is inherently flexible, heat-resistant, and chemically stable. Silicone mold rubbers typically come in two forms: tin-cured and platinum-cured. Tin-cured silicone, known for its ease of use and shorter curing time, is often preferred for quick-turnaround projects. Platinum-cured silicone, while requiring more precise handling, offers superior strength, higher heat resistance, and minimal shrinkage, making it ideal for more demanding prototyping tasks.
Advantages for Prototyping
Flexibility and Detail Replication
One of the most significant advantages of silicone mold rubber in prototyping is its exceptional flexibility. This property allows silicone molds to accurately capture intricate details and complex geometries of the original design, which is crucial in prototyping where precision is paramount. The flexibility also aids in the demolding process, especially for designs with undercuts or delicate features, ensuring the integrity of both the mold and the prototype.
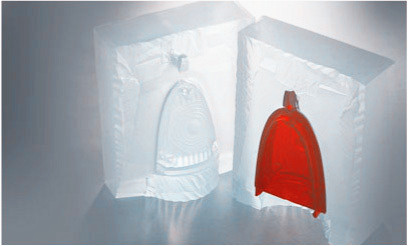
Non-Stick Surface and Chemical Resistance
Silicone’s natural non-stick surface is another boon for rapid prototyping. This characteristic simplifies the mold-making process by reducing the need for a release agent, thereby saving time and preserving the fine details of the prototype. Additionally, silicone is chemically inert, meaning it does not react with most casting materials. This chemical resistance ensures that the prototype’s surface remains unblemished and true to the original design.
Temperature Resistance and Durability
Silicone mold rubbers are capable of withstanding a wide range of temperatures, making them suitable for prototyping materials that require heat during processing. This temperature resistance extends the life of the mold, allowing it to be used repeatedly without degradation. The durability of silicone molds is a key factor in their suitability for quick prototyping, where molds may need to be used multiple times in rapid succession.
In summary, silicone mold rubber’s composition and properties make it an excellent choice for quick prototyping. Its flexibility, non-stick surface, and temperature resistance provide the versatility and efficiency required in the fast-paced world of prototype development.
Common Prototyping Applications
Silicone mold rubber, with its versatile properties, is used in a wide array of prototyping applications across various industries. Here are some common examples:
Consumer Products and Electronics
Silicone molds are extensively used in creating prototypes for consumer products like phone cases, kitchen gadgets, and toys. Their ability to replicate intricate details and textures makes them ideal for these applications. In electronics, silicone molds are used to prototype parts like keypads, seals, and gaskets, where precision and material compatibility are crucial.
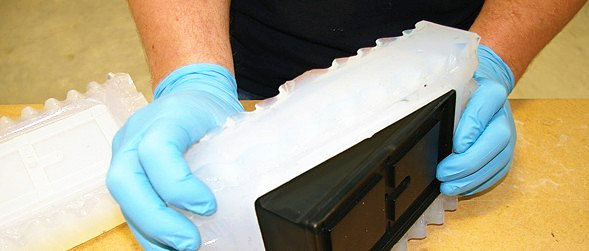
Automotive Parts
In the automotive industry, silicone molds play a pivotal role in prototyping components such as gaskets, seals, and various interior parts. The heat resistance of silicone is particularly beneficial for parts that will be exposed to high temperatures.
Medical Devices
The biocompatibility of silicone makes it a preferred choice for prototyping medical devices. Prosthetics, surgical instruments, and diagnostic tools are often prototyped using silicone molds to ensure safety and accuracy.
Case Studies
Case Study 1: Tech Startup Prototype
A tech startup utilized silicone mold rubber to prototype a new wearable device. The flexibility of silicone allowed for the creation of a skin-safe, comfortable prototype that could be worn for extended periods. This early prototype was instrumental in securing funding and moving the product towards mass production.
Case Study 2: Custom Medical Device
A medical device company used silicone molds to prototype a custom surgical tool. The prototype needed to be precise, sterilizable, and safe for patient contact. Silicone’s properties made it possible to quickly iterate designs, leading to a successful product that improved surgical outcomes.
Case Study 3: Automotive Design
An automotive company employed silicone molds in the rapid prototyping of a new dashboard design. The project required a material that could replicate the texture and feel of the final product. Silicone’s ability to mimic various textures and its durability under repeated handling made it the ideal choice for this application.
These case studies demonstrate the versatility and effectiveness of silicone mold rubber in rapid prototyping, showcasing its ability to meet diverse requirements and contribute significantly to the development and refinement of new products.
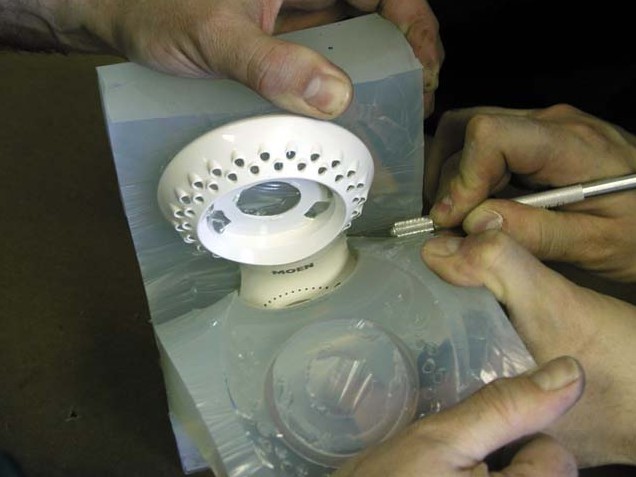
Section 2: Polyurethane Mold Rubber in Prototyping
Composition and Properties
Polyurethane mold rubber is a synthetic material that has become a staple in the prototyping world due to its unique composition and physical traits. It is formed by reacting a polyol with a diisocyanate or a polymeric isocyanate in the presence of suitable catalysts and additives. The result is a versatile elastomer that can be engineered to a wide range of hardness levels, from soft and flexible to hard and rigid. This versatility is achieved by adjusting the chemical formulation, allowing for customization to suit specific prototyping needs.
The physical properties of polyurethane mold rubber are notable for their strength and durability. Polyurethane is known for its excellent tear strength, abrasion resistance, and overall toughness. It can withstand mechanical stress and maintain its integrity over multiple uses, making it an ideal material for producing durable prototypes that require repeated handling and testing.
Advantages for Prototyping
Durability and Resilience
One of the primary advantages of using polyurethane mold rubber in prototyping is its durability. Prototypes made from polyurethane can endure rigorous testing and handling, which is essential in the iterative process of prototype development. This durability ensures that the molds can be used repeatedly without significant wear, providing consistent results across multiple iterations.
Cost-Effectiveness
Another significant advantage of polyurethane in prototyping is its cost-effectiveness. Compared to other mold-making materials, polyurethane is generally more affordable, making it a practical choice for prototyping projects where budget constraints are a consideration. This cost-effectiveness does not come at the expense of quality, as polyurethane molds can produce highly detailed and accurate prototypes.
Versatility in Applications
Polyurethane’s ability to be formulated to different hardness levels and its compatibility with a wide range of casting materials make it a versatile choice for various prototyping applications. Whether it’s for creating rigid industrial parts or more flexible items, polyurethane can be tailored to meet the specific requirements of the prototype.
In summary, polyurethane mold rubber offers a combination of durability, cost-effectiveness, and versatility, making it a valuable material in the field of rapid prototyping. Its ability to produce robust and accurate prototypes efficiently makes it a go-to choice for many professionals in product development and design.
Common Prototyping Applications
Polyurethane mold rubber, with its robust properties, is extensively used in a variety of prototyping applications. Here are some common examples:
Industrial and Mechanical Components
In the industrial sector, polyurethane is often used for prototyping mechanical parts such as gears, valves, and housings. Its strength and resistance to wear make it ideal for parts that must endure stress and strain during testing.
Consumer Goods and Packaging
Polyurethane molds are used in the development of consumer goods, including household items, toys, and packaging prototypes. Its versatility allows for the creation of prototypes ranging from rigid, durable items to those requiring a degree of flexibility.
Automotive Parts
In the automotive industry, polyurethane is used to prototype a variety of components, including dashboards, bumpers, and other interior and exterior parts. These prototypes need to mimic the final product’s strength and durability closely.
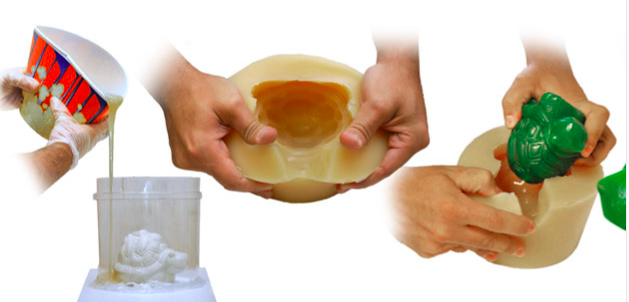
Case Studies
Case Study 1: Industrial Design Firm
An industrial design firm used polyurethane mold rubber to prototype a new line of high-performance sports equipment. The prototypes needed to be strong enough to withstand rigorous testing and use. Polyurethane’s durability and ability to replicate fine details made it the perfect choice for this application.
Case Study 2: Packaging Prototype
A packaging design company utilized polyurethane molds to create prototypes for a new eco-friendly packaging solution. The project required a material that could be easily modified and withstand the rigors of testing different design iterations. Polyurethane provides the necessary durability and flexibility.
Case Study 3: Automotive Prototyping
An automotive company employed polyurethane molds in the rapid prototyping of a new car model’s interior components. The prototypes needed to accurately represent the final product’s look, feel, and durability. Polyurethane’s ability to produce high-quality, resilient prototypes was crucial in the design and testing process.
These case studies demonstrate polyurethane mold rubber’s effectiveness in rapid prototyping, highlighting its ability to meet diverse requirements and contribute significantly to the development and refinement of new products across various industries.
Comparative Analysis: Silicone vs Polyurethane
Direct Comparison
Property | Silicone Mold Rubber | Polyurethane Mold Rubber |
Flexibility | Extremely flexible, ideal for intricate designs | Varies from flexible to rigid, adaptable to different needs |
Durability | High durability, especially in platinum-cured forms | Exceptionally durable, ideal for high-wear applications |
Detail Replication | Excellent for capturing fine details and textures | Very good, with a range suitable for most prototyping needs |
Cost | Generally more expensive | More cost-effective, especially for larger projects |
Curing Time | Varies, generally longer than polyurethane | Relatively quick, advantageous for rapid prototyping |
Chemical Resistance | High, resistant to many chemicals and temperatures | Good, but can be sensitive to certain chemicals |
Ease of Use | Easy to work with, often does not require a release agent | Requires careful handling, often needs a release agent |
Temperature Resistance | Excellent, can withstand high and low temperatures | Good, but may degrade at higher temperatures |
Shelf Life | Long, especially for platinum-cured silicone | Good, but can be affected by environmental factors |
Decision Factors
When deciding between silicone and polyurethane mold rubbers for prototyping, consider the following:
Complexity of Design: If your prototype requires intricate details or undercuts, silicone’s flexibility and detail replication make it a superior choice.
Durability Needs: For prototypes that will undergo extensive testing or handling, polyurethane’s durability and wear resistance are advantageous.
Budget Constraints: If cost is a significant factor, polyurethane offers a more economical solution, especially for larger or multiple prototypes.
Curing Time and Prototyping Speed: Polyurethane’s quicker curing time can be beneficial in rapid prototyping environments where time is of the essence.
Material Compatibility: Consider the materials you will be casting in the mold. Silicone is generally more chemically resistant and less likely to react with casting materials.
Temperature Requirements: For prototypes that will be exposed to extreme temperatures, silicone’s superior temperature resistance is a key advantage.
In summary, the choice between silicone and polyurethane mold rubbers for prototyping depends on a balance of factors including design complexity, durability requirements, budget, and specific project needs. Understanding the strengths and limitations of each material will guide you to the best choice for your prototyping project.
User Experiences and Expert Opinions
Interviews and Quotes
From a Product Designer:
“Silicone molds have been a game-changer for our intricate design prototypes. Their flexibility and detail accuracy are unmatched,” shares Emily Nguyen, a product designer at Innovate Design.
From an Industrial Engineer:
“We often lean towards polyurethane for creating functional prototypes in our industrial applications. Its durability and cost-effectiveness are crucial for our rapid testing cycles,” notes Mark Johnson, an industrial engineer at TechAdvance.
Insights from Developers and Engineers
Product developers and engineers often weigh the pros and cons of silicone and polyurethane based on the prototype’s intended use. Silicone is preferred for its precision and flexibility, especially in consumer products and medical devices. Polyurethane, on the other hand, is favored for its strength and cost-efficiency in industrial components and high-volume projects.
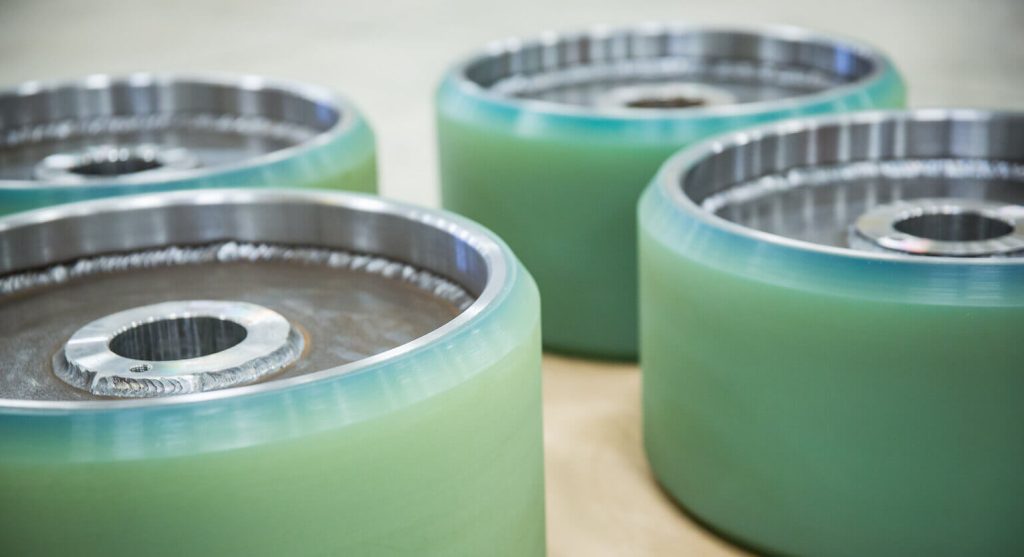
Tips for Effective Prototyping with Mold Rubbers
Best Practices for Using Silicone
Ensure Proper Curing: Allow adequate time for silicone molds to cure completely to ensure the best results.
Utilize Its Flexibility: Take advantage of silicone’s flexibility to create complex and intricate prototypes.
Maintain Clean Surfaces: Keep the mold and casting surfaces clean to preserve the fine details.
Maximizing Efficiency with Polyurethane
Control Environmental Factors: Work in a moisture-controlled environment to ensure the quality of polyurethane molds.
Use Quality Release Agents: Select compatible release agents to ensure easy demolding and surface finish.
Optimize Mix Ratios: Follow the manufacturer’s guidelines for mixing ratios to achieve the desired hardness and properties.
Conclusion
In the debate between silicone and polyurethane mold rubbers for quick prototyping, each material presents its unique strengths. Silicone stands out for its exceptional detail replication and flexibility, making it ideal for complex and delicate prototypes. Polyurethane, with its durability and cost-effectiveness, is well-suited for more robust and high-volume prototyping needs. The choice ultimately hinges on the specific requirements of your project, including design complexity, durability needs, and budget constraints. As a prototyper or product developer, considering both materials and understanding their properties will empower you to make the best decision for your unique prototyping challenges.