Introduction
Polyurethane molding is a versatile process that involves the fabrication of plastic parts by introducing a urethane polymer system into a mold, allowing it to cure. This method is efficient for producing a wide range of consumer goods and industrial parts due to polyurethane’s excellent processability. Polyurethanes can be formulated to have various properties, ranging from soft and pliable to hard and rigid, making them suitable for diverse applications.
What is Polyurethane Molding?
Polyurethane molding is a process where a urethane polymer system is introduced into a tool or mold, which then cures. This material is highly processable, making it efficient for fabricating common consumer goods and industrial parts. Polyurethanes can be formulated to yield different plastic properties, from very soft to hard and rigid. They are used extensively in furniture (like cushions and underlays), construction (for insulation), automotive parts (like bumpers and fenders), and industrial equipment (such as rollers and wheels).
History of Polyurethanes
Polyurethanes were discovered by Otto Bayer in 1937. Initially, polyurethane was intended as a synthetic substitute for natural rubber during World War II due to the high demand for rubber. Its versatility led to its use in textiles, cushions, and metal finishing. The introduction of polyisocyanates in 1952 and polyether polyols in 1956 by DuPont paved the way for the commercial introduction of polyether-based urethane systems, which exhibited excellent processing, stability at low temperatures, and resistance to water and humidity.
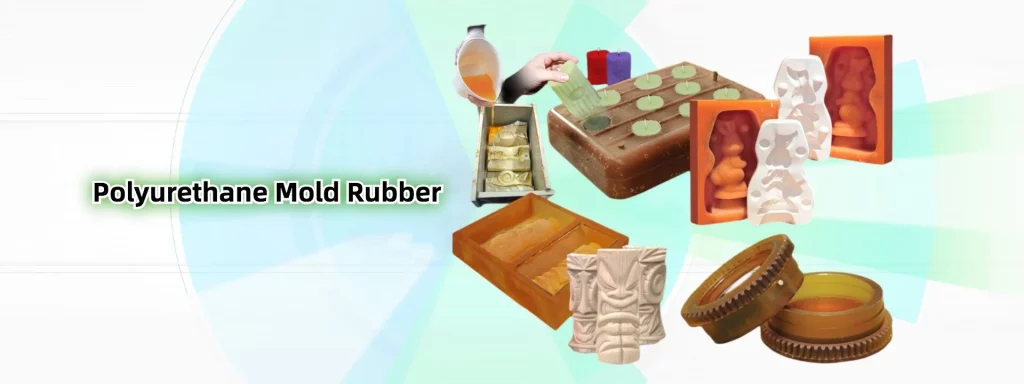
Properties of Polyurethane
Polyurethane is a preferred plastic molding material due to its various desirable characteristics, including hardness, resilience, and chemical resistance. By formulating the polymer system with specific components, polyurethanes can be engineered to have different mechanical and chemical properties. Some of these properties include hardness (measured by the Shore Hardness Number), abrasion resistance, tear strength, impact strength, fatigue resistance, thermal aging resistance, friction, machinability, and chemical resistance.
Molding Processes
There are several molding processes for polyurethane, including:
Injection Molding: Traditional process suitable for both thermoset and thermoplastic polyurethanes.
Reaction Injection Molding: Uses liquid prepolymer components and is limited to producing thermosetting polyurethanes.
Compression Molding: Popular for forming large thermosetting polyurethane products.
Rotational Molding: Produces seamless, hollow products.
Blow Molding: Creates hollow products by inflating a softened preform inside a mold.
Casting: Uses a soft mold, typically made of silicone elastomer, ideal for short-runs and medium-volume production.
Open Cast Molding: Simplest method, ideal for short production runs.
Conclusion
Polyurethane molding is a versatile and efficient process for producing a wide range of products. Its adaptability, combined with its excellent properties, makes polyurethane a preferred choice for various industries. Whether it’s for furniture, construction, automotive, or industrial applications, polyurethane molding offers solutions that cater to specific needs and requirements.