Choosing the Best Rubber for Concrete Molds: Polyurethane vs. Silicone
When it comes to creating molds for concrete casting, the choice of rubber material is crucial. Two of the most popular options are polyurethane and silicone rubber. But which is the best choice for your concrete molding project? Let’s dive into the comparison.
Understanding Polyurethane and Silicone Rubber
Both polyurethane and silicone are thermosetting polymers, commonly used in the molding industry. However, their properties and applications can differ significantly.
Polyurethane Rubber: This is an organic polymer known for its durability and versatility. It’s often recommended for concrete casting projects, such as tiles, panels, statuary, pavers, and more.
Silicone Rubber: An inorganic polymer, silicone rubber boasts excellent release properties and is built on a silicon-oxygen backbone. It’s resistant to UV, ozone, and high temperatures.
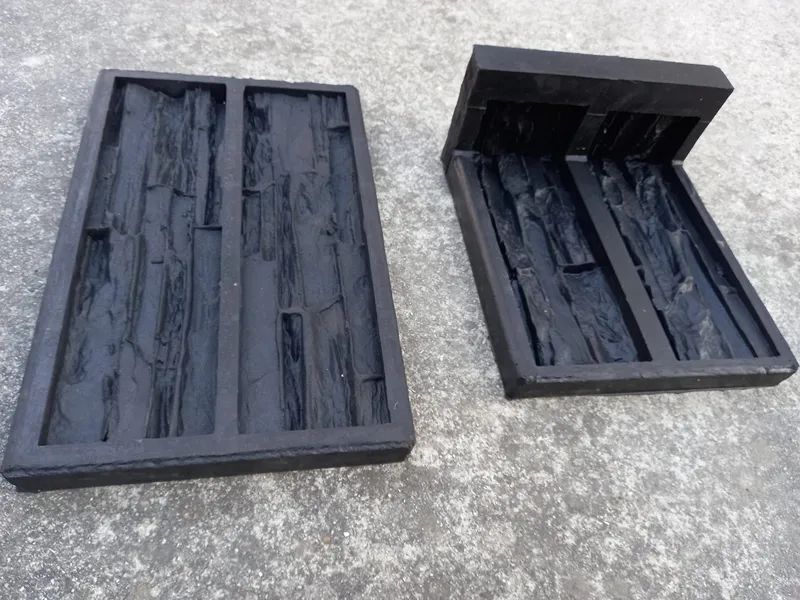
Key Points of Comparison
Efflorescence & Color: Efflorescence, which results in salt deposits on the concrete surface, is more commonly observed when using silicone rubber molds. This white residue can be unsightly and may require solvents for removal. Additionally, concrete cast in polyurethane molds tends to have a more vivid color compared to those cast in silicone molds.
Cost: Silicone rubber is generally more expensive than polyurethane. The cost can be almost double, depending on the specific type and grade of the rubber.
Durability: Polyurethane rubbers are tougher and more resilient than silicones. This makes them more durable, especially when molds are used repeatedly over the years.
Release Properties: Silicone rubbers have superior release qualities, often eliminating the need for release agents. On the other hand, polyurethane molds usually require a release agent, like Pol-Ease® 2650, before casting concrete.
Hardness Range: Polyurethane rubber offers a broader hardness range, with options available up to a Shore D45. In contrast, the hardest silicone option from many manufacturers might only go up to a Shore A60.
Applications Polyurethane vs. Silicone
Polyurethane Rubber: Given its durability, polyurethane is ideal for projects that require repeated use of the mold. It’s perfect for creating concrete tiles, panels, bricks, countertops, and more.
Silicone Rubber: While silicone can also be used for concrete casting, it’s often chosen for projects that require intricate details due to its excellent release properties. It’s suitable for decorative tabletops, ornate designs, and other detailed projects.
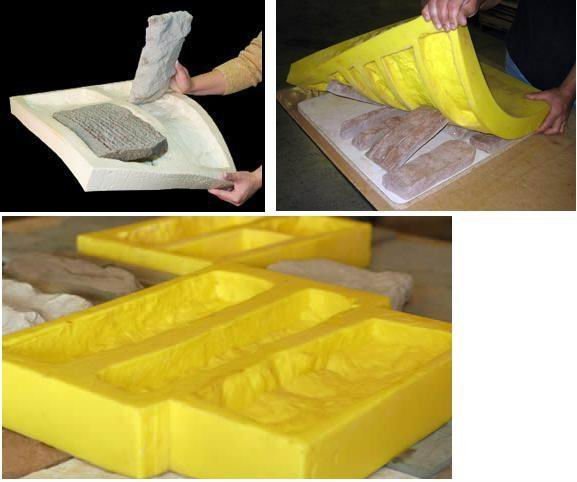
Environmental Impact and Sustainability
Both polyurethane and silicone are thermosetting polymers. This means that they break down into harmful chemicals if heated beyond their maximum operating temperatures. They also don’t resolidify like thermoplastics. As a result, recycling these materials is challenging. Most recycling facilities lack the capability to recycle these materials economically. Both materials are not considered sustainable as they aren’t derived from renewable resources.
Conclusion
While both polyurethane and silicone rubber have their merits, the choice largely depends on the specific requirements of the project. For projects that demand durability and repeated use of the mold, polyurethane is the preferred choice. Its resilience to wear and tear ensures that the mold remains in good condition even after multiple uses.
On the other hand, if the project requires intricate details and a smooth finish, silicone rubber, with its excellent release properties, might be the better option. However, it’s essential to be aware of the potential for efflorescence and the muted color that might result from using silicone molds.
In conclusion, when choosing the best rubber for concrete molds, it’s crucial to consider the project’s requirements, budget, and desired outcome. Both polyurethane and silicone rubber offer unique advantages, and understanding their properties can help in making an informed decision.